زمانی که برای اولین بار کار مهندسی مکانیک رو شروع کردم، خیلی زود فهمیدم که طراحی فقط کشیدن و نقاشی کردن در نرم افزار کتیا، و سالیدورک نیست.لازم که در نظر داشته باشیم اگر باید چیزی طراحی کنیم، باید و باید به ساختش فکر کنیم، یعنی طراحی بر پایه ساخت ولی خب در ایران خیلی و خیلی روش ساخت داریم که نمیتونیم تو هیچ مقاله اون حجم از اطلاعات رو در یک پست بگنجونیم، پس در این پست به روش تولید قطعات پلاستیکی در صنعت ایران میپردازیم.
خوبه که بدونیم تنها راه تولید قطعات پلاستیکی صرفا پرینتر سه بعدی نیست و روش های زیادی برای اینکار داریم.
در عکس پایین روش تولید قطعات پلاستیکی رو به هشت مورد اصلی اختصاص دادیم، بریم ببینیم کدوم روش برای ما کاربرد داره ولی قبلش باید چند تا سوال رو جواب بدیم.

چقدر قطعه ما جزییات ریز داره ؟
اندازه قطعه چقدره ؟
چقدر تلرانس برای ما قابل قبول ؟
کدوم روش تولید توانایی ساخت قطعه مارو داره ؟
چه تعداد از قطعه لازم داریم ؟
ایا روش مورد نظرمون امکان تولید محدود رو داره ؟
چه تعداد از قطعه برای استارت دستگاه کافیه ؟
برای تولید فقط یک قطعه کدوم روش خوبه ؟
هزینه ها در تولید تیراژ به مراتب کمتر میشه پس کدوم روش مناسب ماست ؟
ایا پولش رو خودمون میدیم یا در قالب یک شرکت پرداخت میکنیم؟پول استارت دستگاه چقدره ؟
ایا میصرفه در تیراژ قطعه تولید کنیم ؟
جنس ما باید چه الزامات مکانیکی و شیمیایی رو پاس کنه ؟
کدوم پلاستیک قابل دسترس و نیاز مارو برطرف میکنه؟
ایا ماده ای که ما میخواهیم در ایران وجود دارد؟ یا از طریق مرز باید وارد ایران بشه ؟
مهمترین سوال مشتری و مهمترین دارایی انسان : چقدر زمان میبره ؟
برای تیراژ بالا چه مقدار زمان لازمه ؟
اگه برای مثال چند نمونه اولیه بخواهیم چقدر زمان میبره تا بدستمون برسه ؟
ترموپلاستیک :
میتوان آنهارا بارهای ذوب و منجمد کرد فرایند برگشت پذیری دارند.و هیچ اتصال شیمایی بین آنها نیز اتفاق نمی افتد.انواع مختلفی دارند.
- اکریلیک (PMMA)
- آکریلونیتریل بوتادین استایرن (ABS)
- پلی آمید (PA)
- پلی لاکتیک اسید (PLA)
- پلی کربنات (PC)
- پلیاتراترکتون (PEEK)
- پلی اتیلن (PE)
- پلی پروپیلن (PP)
- پلی وینیل کلراید (PVC)
ترموست :
زمانی که شکل بگیرند دیگر نمیتوان آنها را به شکل اولیه دراورد، و فرایند برگشت ناپذیری دارند، بین آنها پیوند شیمیایی شکل میگیرد
- فنول فرمالدهید (با نام تجاری باکالیت)
- اوره فرمالدهید
- سیانات استر
- اپوکسی
- پلی استر
- پلی اورتان
- سیلیکون
- لاستیک ولکانیزه
1. معرفی روش cnc پلاستیک
خب ممکن به عنوان یک سازنده کمو بیش اسم دستگاه های CNC به گوشتون خورده باشه، قبلا هم به طور مفصل درباره طرز کار دستگاه های CNC صحبت کرده بودیم، باز اشاره ای مختصر بهش میکنیم
به طور کلی دو روش تولید با دستگاههای cnc داریم : تراش و فرز
که به صورت دستی و اتوماتیک میتوان از این روش استفاده کرد، دایره وسیعی از مواد ها مختلف رو در اختیار ما قرار میدهد.
این فرایند ها با بلوک های جامد، میله های فلزی یا پلاستیکی شروع می شوند که طی آن، قطعات با حذف مواد از طریق برش، فرز، سوراخ کردن و سنگ زنی شکل می گیرند.
بر خلاف اکثر فرایندهای تولید پلاستیک، ماشینکاری CNC یک فرایند ساخت کاهشی است که در آن بلوک یا توسط یک ابزار چرخشی و قطعه ثابت، یا یک قطعه چرخشی و ابزار ثابت حذف می شوند.
در این فرایند مانند همه فرایندهای ساخت نیاز به پرداخت سطح خروجی داریم.
ماشینکاری برای ساخت قطعات پلاستیکی با حجم کم و هندسه هایی که قالب گیری آنها دشوار است گزینه ایده آلی می باشد. کاربردهای معمول ماشینکاری شامل ساخت نمونه های اولیه و قطعات نهایی مانند قرقره ها، چرخ دنده ها و بوش ها است.
ماشینکاری CNC هزینه نصب و راه اندازی کم تا متوسطی دارد و می تواند قطعات پلاستیکی با کیفیت بالا را در مدت زمان فرآوری کوتاهی و با استفاده از طیف گسترده ای از مواد تولید کند.
در ایران دستگاه های cnc رو به تعداد محورهاشون دسته بندی میکنند،معمولا 3 محور تا شش محور تقسیم بندی میشوند ، که cnc 3 محور رایجترین cnc بین دستگاهای فرز سی ان سی است.
هر چی قطعه پیچیده تر، هزینه تولید نیز بیشتر میشود، بر خلاف پرینتر سه بعدی که تفاوتی ندارد که چه هندسه ای دارد
اکریلیک (PMMA)
آکریلونیتریل بوتادین استایرن (ABS)
پلی آمید (PA)
پلی لاکتیک اسید (PLA)
پلی کربنات (PC)
پلیاتراترکتون (PEEK)
پلی اتیلن (PE)
پلی پروپیلن (PP)
پلی وینیل کلراید (PVC)
پلی کربنات (PC)
پلی استایرن (PS)
پلی استال (POM)
2.معرفی روش ریخته گری پلیمر (سیلیکون)
سیلیکون یک انتخاب قوی برای ساخت قالب است زیرا مزایای بسیار متنوعی را در اختیار شما قرار می دهد. با استفاده از قالب سیلیکون می توانید به راحتی طرح های سفارشی ایجاد کنید. خود قالب ها نیز کاملاً بادوام هستند ، بنابراین می توانید بدون ترس از شکستگی آنها را به طور مکرر استفاده کنید.
قالب های چاپ شده سه بعدی برای قطعات سیلیکونی
اگر محصول نهایی شما از سیلیکون ساخته شده باشد ، قالب های چاپ سه بعدی برای شما ایده آل است. سیلیکون با قالبهای پلاستیکی تداخل و واکنش نشان نمی دهد ، تنها نکته مهمی که باید بخاطر بسپارید نقطه ذوب پلاستیک است. برخی از مواد حتی در برابر حرارت نیز مقاوم هستند که آنها را کاندید مناسبی برای قالب های چاپ سه بعدی می کند. تولید قالب سریع و آسان انجام خواهد شد. به لطف قالب های چاپ شده ، قطعات سیلیکونی شما نرم و صاف می شوند و می توانند جزئیات زیادی داشته باشند. قالب های چاپ سه بعدی نیز مقاوم هستند و به راحتی می توان چندین بار از آنها استفاده کرد. این یک روش شگفت انگیز برای بهبود روند ساخت است.
پلیمرهای معمول برای ریخته گری شامل پلی اورتان، اپوکسی، سیلیکون و اکریلیک هستند.
آماده سازی قالب:
در این مرحله قالب با یک عامل آزاد کننده جهت سهولت جدا کردن قالب پوشش داده می شود و اغلب تا دمای ویژه یک ماده گرم می شود.
ریخته گری:
رزین مصنوعی با یک عامل پخت مخلوط شده و در قالب ریخته یا تزریق می شود تا جایی که فضای داخلی قالب را پر می کند.
پخت:
عملیات پخت آغاز می شود تا زمان جامد شدن ادامه می یابد. (قرار دادن قالب در معرض حرارت می تواند باعث تسریع زمان پخت برخی از پلیمرهای خاص شود).
جداسازی قالب:
قالب باز شده و قطعه پخته شده جدا می شود.
اصلاح:
پلیسه ها، راهگاه ها و شکاف ها برش داده می شوند یا از بین می روند.
قالب های انعطاف پذیر ساخته شده از لاستیک لاتکس یا لاستیک سیلیکونی ولکانیزه شده در دمای اتاق (RTV) در مقایسه با ابزار سخت ارزان هستند اما فقط تعداد محدودی (حدود ۲۵ تا ۱۰۰) ریخته گری را می توانند انجام دهند
زیرا واکنش شیمیایی اورتان ها، اپوکسی ها، پلی استر و اکریلیک سطح قالب را تخریب می کند.
قالب های سیلیکونی RTV می توانند حتی کوچکترین جزئیات را تولید کنند و قطعات ریخته گری با کیفیت بالایی را ارائه دهند.
ریخته گری پلیمر روشی نسبتاً ارزان می باشد که به سرمایه گذاری اولیه اندکی نیاز دارد، اما پلیمرهای ترموست برای ریخته گری معمولاً گرانتر از نمونه های ترموپلاستیک هستند.
هر قطعه ریخته گری برای عملیات پس پردازش به نیروی کار عملی نیاز دارد که هزینه نهایی هر قطعه را در مقایسه با روشهای تولید خودکار مانند تزریق پلاستیک بالا می برد.
روش ریخته گری پلیمر معمولاً برای نمونه سازی، تولید کوتاه مدت و همچنین برخی از کاربردهای دندانپزشکی و جواهرات استفاده می شود.
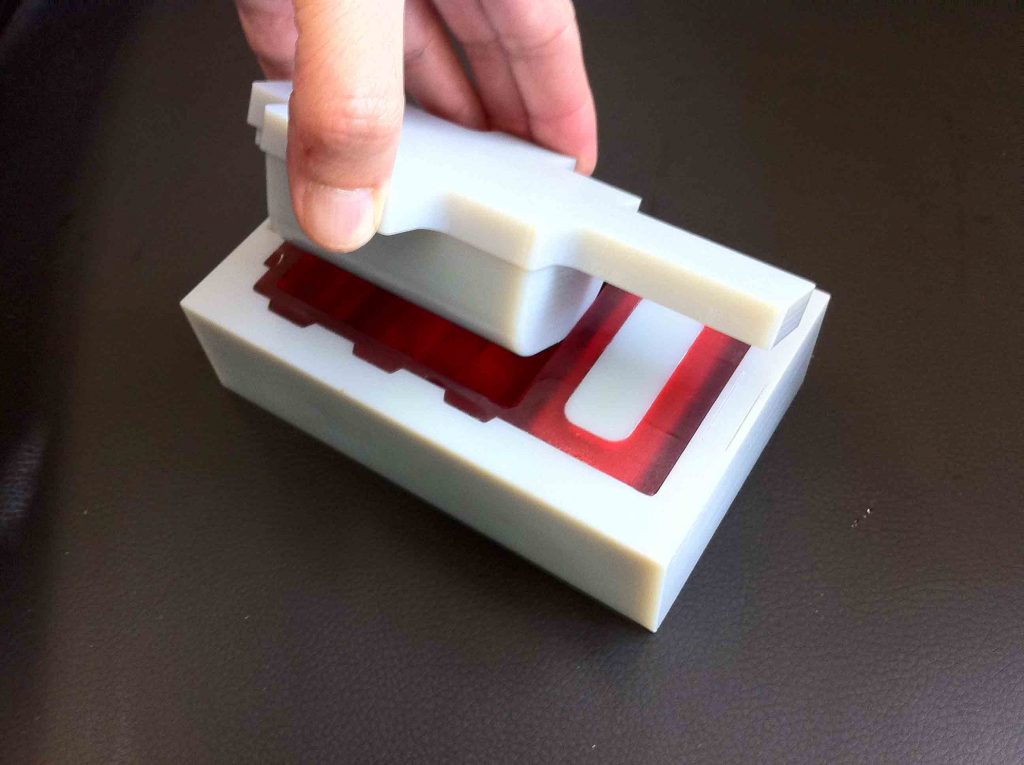
به نامهای Rotomolding , Rotocasting شناخته میشود.
این روش، فرآیندی برای تولید قطعات پلاستیکی تو خالی است. رقابتهایی بین این دو روش و روشهای قالبگیری دمشی، گرماشکلدهی و قالبگیری تزریقی وجود دارد.
البته قالبگیری چرخشی مزایای ویژهای از جمله میزان کمتنشهای پس ماند و قالبهای نسبتاً ارزان را دارا است.
علاوه بر این از نظر تولید قطعات یک تکه، توخالی و بزرگ (بزرگتر از ۲ متر مکعب) رقبای کمی در برابر این روش وجود دارد.
این روش بیشتر برای تولید مخازن شناخته شدهاست اما میتواند برای تولید محصولات پزشکی پیچیده، اسباب بازیها و دیگر وسایل بکار رود.
پر کردن قالب یا charging
مقدار معینی پودر پلاستیک در حفره قالب ریخته می شود و سپس قسمتهای باقی مانده قالب نصب شده و حفره برای گرم شدن بسته می شود.
حرارت دهی یا heating
قالب تا زمانی که پودر پلاستیک ذوب شود و به دیواره های قالب بچسبد گرم می شود، در این مرحله به منظور اطمینان از ایجاد یک پوشش پلاستیکی یکنواخت، قالب در امتداد دو محور عمود بر هم چرخانده می شود.
خنک سازی یا cooling
سپس قالب به آرامی سرد می شود، در این مرحله جهت جلوگیری از ته نشینی و یا ریزش پودر، قالب همچنان درحال چرخش باقی می ماند.
جداسازی قطعه
پس از سرد شدن، چرخش قالب متوقف شده و قطعه از قالب جدا می شود.
قالب گیری چرخشی دارای برخی محدودیت های طراحی است و محصولات نهایی دارای تلرانس بارزتری هستند. از آنجا که کل قالب باید گرم و سرد شود، این فرایند دارای چرخه زمانی طولانی است و نیاز به نیروی کار زیادی دارد که کارایی آن را برای کاربردهای با حجم بالاتر محدود می کند.
پلی اتیلن
پلی پروپیلن
پلی وینیل کلراید
نایلون
- پلی کربنات
- روش عالی برای تولید قطعات پلاستیک تو خالی
- کم بودن هزینههای مربوط به تجهیزات و راه اندازی آن نسبت به قالب گیری بادی
- امکان خارج نمودن آسان قطعه از قالب
- کنترل آسان ضخامت دیواره
- یکنواختی ضخامت دیواره و خطای بسیار کم در این یکنواختی
- توانایی تولید قطعات سه لایه و قطعات دوجداره با ثبات
- زمان نسبتاً کوتاه در ساخت قالب دستگاه
- ناچیز بودن میزان ضایعات پلاستیک (بسته به نوع رزین)
- مقاومت بالای فیزیکی و شیمیایی
- امکان تعویض سریع قالب در کوتاه ترین زمان
- تحت فشار نبودن این ماده در این روش
- استفاده مجدد از قطعات تولید شده پس از مصرف
- امکان قالب گیری چند مادهی یکسان یا مشابه
زمان طولانی تولید محصول
مناسب نبودن برای تولید قطعات کوچک در تیراژ بالا
محدودیت در انتخاب مواد اولیه
هزینه نسبتاً زیاد مواد اولیه
حالت فیزیکی مواد اولیه باید مایع و به صورت
پودرهای ریز باشد
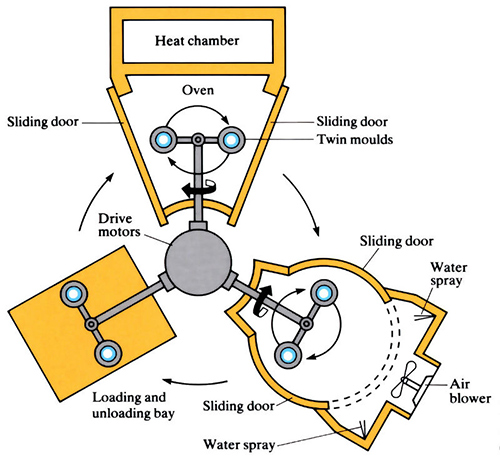
معرفی روش شکل دهی با خلأ یا وکیوم فورمینگ
وکیوم فرمینگ چیست:
ترمو فرمینگ یا شکل دهی حرارتی, یکی از روشهای پرکاربرد شکل دهی پلاستیک ها است . در این فرآیند ابتدا ورق پلاستیکی گرما نرم (ترموپلاست ) آنقدر حرارت می بیند تا نرم و انعطاف پذیر شود. سپس این ورق روی قالب گذاشته شده و با اعمال فشار هوا یا ایجاد خلا و یا به صورت مکانیکی روی قالب کشیده می شود و شکل قالب را به خود می گیرد.
وکیوم فرمینگ پلاستیک یکی از زیر شاخه های فرآیند ترموفرمینگ برای شکل دهی پلاستیک ها می باشد.
وکیوم فرمینگ اولین و ساده ترین فرایند شکل دهی حرارتی می باشد .
بسیاری از قطعات پلاستیکی از ظروف یک بار مصرف تا طلق های بسته بندی محصولات و یا حتی داشبورد خودرو به روش ترموفرمینگ و یا وکیوم فرمینگ ساخته می شوند.
تمامی ورقهای گرما نرم (ABS, PVC, PET.هایمپکت .کریستال و…) قابلیت شکل پذیری را دارند.
هزینه ابزارآلات در روش وکیوم فورمینگ به دلیل نیروها و فشارهای کم در مقایسه با سایر تکنیک های قالب سازی کم است. قالب ها برای تولید کوتاه مدت و قطعات سفارشی از چوب، گچ یا رزین های پرینت سه بعدی ساخته می شوند. تولید کنندگان برای تولید در حجم بالا از ابزارآلات فلزی با دوام تر استفاده می کنند.
- صنعت بسته بندی (ظروف یکبار مصرف، استند محصولات آرایشی و شیرینی و شکلات)
- کشاورزی (سینی های کاشت بذر، گلدان)
- – صنعت خودرو (قطعات تزئینی داخل خودرو)
- – صنایع پزشکی و بیمارستانی ( ماسک رادیو تراپی و سوختگی، قطعات پروتز)
- – اسباب بازی و وسایل ایمنی وزشی
- – قایق سازی
- – وسایل خانه و آشپر خانه (جای قاشق چنگال، )
- – تبلو سازی (تولید حروف و اشکال برجسته)
- – صنایع الکترونیک (سینی های آنتی استاتیک)
- – صنایع بهداشتی (لوازم حمام و …)
آکریلونیتریل بوتادین استایرن (ABS)
پلی اتیلن ترفتالات گلیکول (PETG)
پلی پروپیلن
(PP)
پلی استایرن
(PS)
پلی اتیلن
(PE)
اکریلیک
(PMMA)
پلی وینیل کلراید
(PVC)
پلی کربنات
(PC)